随着《工业互联网创新发展行动计划》(2021~2023)的发布,标志着未来3年将是中国工业互联网快速成长期的关键期。
Industrial IOT
Build an industrial Internet with advanced sensing, real-time control and communication capabilities
When using the industrial Internet to integrate information infrastructure and automation into factories and modern systems, flexibility, integration, intelligent sensing and more functional security features are required.
In robot and other industrial applications, using accurate real-time control can achieve lower power consumption and higher efficiency. TI’s wireless connectivity and multi protocol products play an important role in intelligent manufacturing, which can realize the interaction between workers, robots and other obstacles in the warehouse.
With a series of precision sensing technologies, TI can provide advanced signal processing functions to achieve accurate real-time control and communication. Our industrial communication technology support, such as IO Link and EtherCAT, can not only improve scalability, but also help simplify the transition to intelligent production systems and intelligent manufacturing.
In order to maintain competitiveness and grow, many enterprises are increasingly inclined to maximize work efficiency, economies of scale and quality through advanced industrial automation. An increasingly interconnected world will inevitably connect factories and workshops. Human machine interface (HMI), programmable logic controller (PLC), motor control and sensors need to be connected in a scalable and efficient way.
In the past, many industrial components were controlled by CAN and Modbus ®、 PROFIBUS ® Connect with different serial field bus protocols such as CC Link. In recent years, industrial Ethernet has become increasingly popular, and its applications are everywhere. While increasing the speed, it has expanded the connection distance, and can connect more nodes. Driven by different industrial equipment manufacturers, many different industrial Ethernet protocols are contending. These protocols include EtherCAT, PROFINET, EtherNet/IP and Sercos. Time Sensitive Network (TSN) is also increasingly popular in the field of industrial Ethernet communication. In this article, we will discuss in detail multiple industrial Ethernet protocols and the growing demand for unified hardware and software platforms that support multiple standards and provide real-time, deterministic, and low latency features required for industrial communications.
Introduction to Industrial Automation Components
The realization of industrial automation requires four main components, including PLC controller, HMI panel, industrial driver and sensor.
PLC controller is the brain of industrial automation system; It provides relay control, motion control, industrial input and output processing control, distributed system and networking control functions. PLC often needs to work under harsh environmental conditions, withstand hot, cold, humid, vibration and other extreme conditions, and provide accurate, deterministic and real-time control functions for other parts of the industrial automation system through reliable communication links.
HMI is a graphical user interface for industrial control. It can provide command input and feedback output interface for controlling industrial machinery. The HMI is connected to other parts of the industrial system via a common communication link.
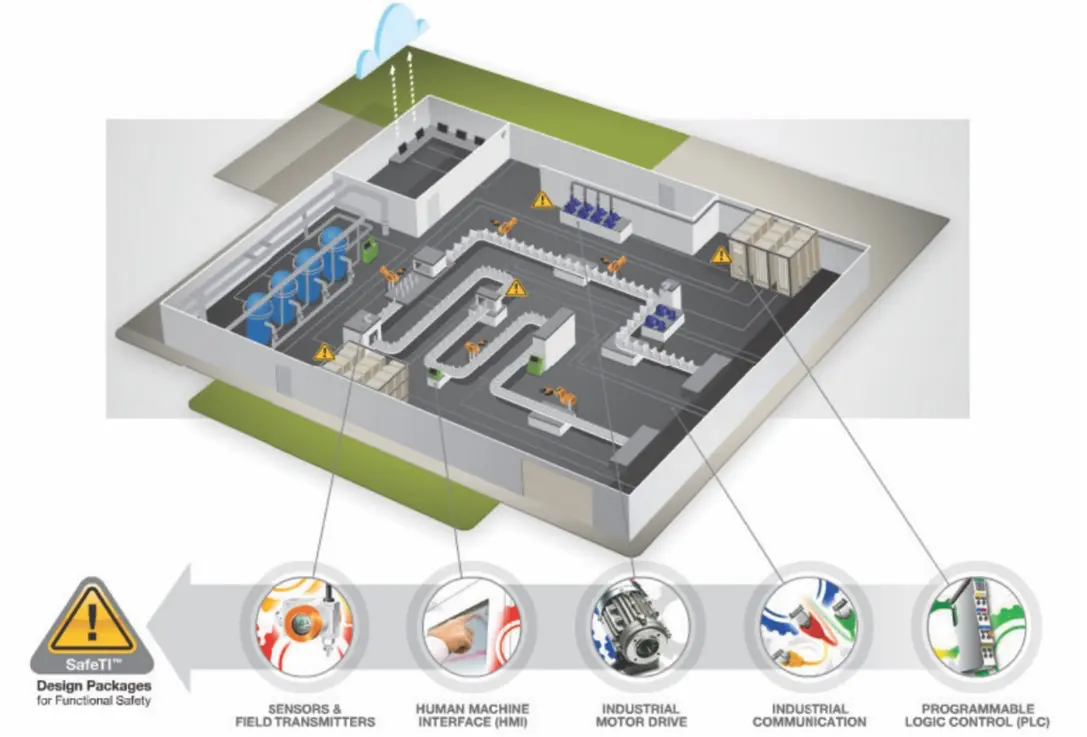
Figure 1. Industrial automation elements and communication links.
Industrial drives are motor controllers for ideal motor operation. They are widely used in various industrial applications and can support a variety of voltage and power consumption levels. Industrial drives include, but are not limited to, AC and DC drives and servo drives that use motor feedback systems to control and adjust the behavior and performance of servo mechanisms.
Sensors are the hands and feet of industrial automation systems, which can monitor industrial operation status, inspection and measurement in real time. They are an indispensable part of industrial automation systems and can provide trigger points and feedback for system control. To build an efficient automatic production system through industrial components, effective communication is indispensable. The example in Figure 1 illustrates the principle that all elements work together through a communication link.
Traditional industrial communication protocol
In the past, people carried out industrial communication on serial interfaces, which were initially created by different companies and later became standards, so many different standards emerged in the market. Because these standards are supported by large enterprises, industrial automation equipment companies need to implement multiple protocols in an industrial system. Due to the long life cycle of industrial systems, including PROFIBUS ®、 CAN bus, Modbus ® And CC Link ® Many serial based protocols including master-slave configuration are still very popular.
PROFIBUS is a more successful field bus technology in the world, which is widely deployed in industrial automation systems including factory and process automation. PROFIBUS provides digital communication for process and auxiliary data at speeds up to 12 Mbps and supports up to 126 addresses.
The control area network (CAN) bus is a highly integrated serial bus system. It was initially created as an automatic vehicle bus, and later became a field bus for industrial automation. It can provide physical layer and data link layer for serial communication, with the speed up to 1Mbps. CANopen ® And DeviceNet are higher level standardized protocols above the CAN bus, which CAN achieve interoperability with devices in the same industrial network. CANopen supports 127 nodes in the network, while DeviceNet supports 64 nodes in the same network.
Modbus is a simple and powerful serial bus. It is publicly released without patent fees. Up to 247 nodes can be connected in the link. Modbus is easy to implement and operates on RS-232 or RS-485 physical links at speeds up to 115K baud. Originally developed by Mitsubishi, CC Link is a popular open architecture industrial network protocol in Japan and Asia. CC Link is based on RS-485 and can connect up to 64 nodes in the same network at a speed of up to 10Mbps.
Industrial Ethernet communication protocol
Ethernet is ubiquitous and cost-effective, with common physical links and faster speeds. Because of this, a variety of industrial communication protocols are being transferred to Ethernet based solutions. Ethernet communication supporting TCP/IP is usually uncertain, and the response time is usually about 100ms. Industrial Ethernet protocols use a modified Medium Access Control (MAC) layer to achieve very low latency and deterministic response. Ethernet also enables the system to have flexible network topology and flexible number of nodes. Let’s learn more about some popular industrial Ethernet communication protocols.
EtherCAT was originally developed by Beckhoff to support high-speed packet processing and provide real-time Ethernet for automation applications. It also provides scalable connections for the entire automation system from large PLC to I/O and sensor levels. EtherCAT is a protocol optimized for process data, using standard IEEE 802.3 Ethernet frames. Each slave node will process the data telegram and insert new data into the frame as each frame passes. This process is processed in the hardware, so each node needs minimal processing delay, which can achieve extremely short response time. EtherCAT is a MAC layer protocol, which is transparent to any higher level Ethernet protocol such as TCP/IP, UDP, Web server, etc. EtherCAT can connect up to 65535 nodes in the system, while the EtherCAT master can be a standard Ethernet controller, simplifying network configuration. Each slave node has low latency, so EtherCAT can provide a flexible, low-cost and network compatible industrial Ethernet solution.
EtherNet/IP is an industrial Ethernet protocol originally developed by Rockwell. Unlike EtherCAT, which is a MAC layer protocol, EtherNet/IP is an application layer protocol over TCP/IP. EtherNet/IP uses the standard Ethernet physical layer, data link layer, network layer and transport layer, and uses the Common Industrial Protocol (CIP) over TCP/IP. CIP provides a set of general messages and services for industrial automation control systems, which can be used for a variety of physical media. For example, CIP on CAN bus is called DeviceNet, CIP on private network is called ControlNet, and CIP on Ethernet is called EtherNet/IP.
EtherNet/IP establishes communication from one application node to another through one TCP connection and multiple CIP connections. Multiple CIP connections can be established through one TCP connection. EtherNet/IP uses standard EtherNet and switches, so it has unlimited number of nodes in the system. In this way, a network can be deployed across multiple different endpoints of the factory floor. EtherNet/IP provides complete producer consumer services, and can achieve very efficient peer to peer communication between slave stations. EtherNet/IP is compatible with many standard Internet and Ethernet protocols, but its real-time and deterministic functions are limited.
PROFINET is an industrial Ethernet widely used by major industrial equipment manufacturers such as Siemens and GE. It has three different categories. PROFINETA class can access PROFIBUS network through proxy, and bridge Ethernet and PROFIBUS with remote procedure call over TCP/IP. Its cycle time is about 100ms, mainly used for parameter data and cyclic I/O. Typical applications include infrastructure and building automation. PROFINET class B, also known as PROFINET real-time (PROFINET RT), introduces a software based real-time method and reduces the cycle time to about 10ms. Class B is usually used for factory automation and process automation. PROFINET Class C (PROFINET IRT) is an isochronous real-time transmission, which requires special hardware to reduce the cycle time to less than 1ms, so as to provide the performance required for motion control operation in real-time industrial Ethernet.
PROFINET RT can be used for PLC type applications, while PROFINET IRT is very suitable for sports applications. Branches and stars are common topologies of PROFINET. If you want to make the PROFINET network achieve the required system performance, you need to carefully carry out topology planning.
POWERLINK was originally developed by B&R. Ethernet POWERLINK is adopted on IEEE 802.3, so network topology, cross connection and hot plug can be freely selected. It uses polling and time slicing mechanisms to achieve real-time data exchange. The POWERLINK master station or “managed node” controls the time synchronization within tens of nanoseconds through packet jitter. This type of system is applicable to various automation systems ranging from PLC to PLC communication and visualization to motion and I/O control. Open source stack software is available, so there are few obstacles to implementing POWERLINK. In addition, CANopen is a standard component, which makes it easy to upgrade the system from the previous fieldbus protocol. Sercos III is the third generation serial real-time communication system (Sercos). It combines high-speed packet processing capabilities to provide real-time Ethernet and standard TCP/IP communications to build low latency industrial Ethernet.
Much like EtherCAT, data packets are processed from Sercos III by quickly extracting data and inserting it into Ethernet frames to achieve low latency. Sercos III divides the input data and output data into two frames. The cycle time starts from 31.25 microseconds, which is as fast as EtherCAT and PROFINET IRT. Sercos III supports ring or line topology. A major advantage of using a ring topology is communication redundancy. Even if the ring is broken due to a slave node failure, all other slave nodes can still obtain Sercos III frames containing input/output data. Sercos III can have 511 slave nodes in a network, mainly used for servo driver control.
Time Sensitive Network (TSN) is an extension of Ethernet defined by the Institute of Electrical and Electronics Engineers (IEEE), aiming to make Ethernet based network more deterministic. TSN is a local area network (LAN) level solution that can work with non TSN Ethernet, but timeliness can only be guaranteed within the TSN LAN. You can group TSN standards according to the use cases solved by TSN: general time view, guaranteed great delay, or coexistence with background traffic or other traffic. Like any popular standard, TSN’s standard toolbox is also evolving.
Industrial Communication Mechanism of Texas Instruments (TI)
In order to enable industrial equipment manufacturers to implement various industrial communication protocols in an economical and flexible manner, Texas Instruments (TI) has integrated a low latency programmable real-time unit industrial communication subsystem (PRU-ICSS) on a variety of on-chip systems. Compared with FPGA, ASIC and other backup solutions, PRU-ICSS can provide more cost-effective and future oriented flexible solutions for industrial communications. By integrating PRU-ICSS into a single chip, TI’s flexible hardware platform helps manufacturers create more cost-effective, deterministic and efficient software programmable industrial automation systems.
Future trends
We are at the beginning of the fourth industrial revolution, and industrial automation will once again become a driving factor for economic development. The success of industrial automation depends on reliable and efficient communication networks that connect all parts of the plant for efficient operation. The popularity and applicability of Ethernet will continue to stimulate traditional factories to upgrade to industrial Ethernet.
Many different industrial Ethernet protocols have been implemented on site, and each protocol has its own advantages and disadvantages. In the future, industrial Ethernet protocols will continue to develop and integrate to create a real-time, deterministic and stable communication link with higher reliability and integrated security. Ethernet also requires a general programmable hardware platform, such as Sitara with integrated PRU-ICSS introduced by Texas Instruments (TI) ™ Processor to build low-cost flexible systems. The system supports the forward-looking implementation of multiple protocols and new protocols, and can provide an industrial communication engine for industrial automation.