标志着未来3年将是中国工业互联网快速成长期的关键期。
IdO industriel
Construisez un Internet industriel doté de capacités avancées de détection, de contrôle en temps réel et de communication.
Lorsque l’on utilise l’Internet industriel pour intégrer l’infrastructure de l’information et l’automatisation dans les usines et les systèmes modernes, la flexibilité, l’intégration, la détection intelligente et des fonctionnalités de sécurité plus fonctionnelles sont nécessaires.
Dans les robots et autres applications industrielles, l’utilisation d’un contrôle précis en temps réel peut permettre d’obtenir une consommation d’énergie inférieure et une efficacité plus élevée. La connectivité sans fil et les produits multiprotocoles de TI jouent un rôle important dans la fabrication intelligente, qui peut réaliser l'interaction entre les travailleurs, les robots et autres obstacles dans l'entrepôt.
Grâce à une série de technologies de détection de précision, TI peut fournir des fonctions avancées de traitement du signal pour obtenir un contrôle et une communication précis en temps réel. Notre support technologique de communication industrielle, tel que IO Link et EtherCAT, peut non seulement améliorer l'évolutivité, mais également contribuer à simplifier la transition vers des systèmes de production intelligents et une fabrication intelligente.
Afin de maintenir leur compétitivité et de croître, de nombreuses entreprises sont de plus en plus enclines à maximiser l’efficacité du travail, les économies d’échelle et la qualité grâce à une automatisation industrielle avancée. Un monde de plus en plus interconnecté reliera inévitablement les usines et les ateliers. L’interface homme-machine (IHM), l’automate programmable (PLC), la commande moteur et les capteurs doivent être connectés de manière évolutive et efficace.
Dans le passé, de nombreux composants industriels étaient contrôlés par CAN et Modbus ®、 PROFIBUS ® Connect avec différents protocoles de bus de terrain série tels que CC Link. Ces dernières années, l'Ethernet industriel est devenu de plus en plus populaire et ses applications sont partout. Tout en augmentant la vitesse, il a élargi la distance de connexion et peut connecter plus de nœuds. Sous l’impulsion de différents fabricants d’équipements industriels, de nombreux protocoles Ethernet industriels sont en concurrence. Ces protocoles incluent EtherCAT, PROFINET, EtherNet/IP et Sercos. Le Time Sensitive Network (TSN) est également de plus en plus populaire dans le domaine de la communication Ethernet industrielle. Dans cet article, nous aborderons en détail plusieurs protocoles Ethernet industriels et la demande croissante de plates-formes matérielles et logicielles unifiées prenant en charge plusieurs normes et fournissant les fonctionnalités en temps réel, déterministes et à faible latence requises pour les communications industrielles.
Introduction aux composants d'automatisation industrielle
La réalisation de l'automatisation industrielle nécessite quatre composants principaux, dont un contrôleur PLC, un panneau IHM, un pilote industriel et un capteur.
Le contrôleur PLC est le cerveau du système d’automatisation industrielle ; Il fournit des fonctions de contrôle de relais, de contrôle de mouvement, de contrôle du traitement des entrées et sorties industrielles, de systèmes distribués et de contrôle de réseau. L'API doit souvent fonctionner dans des conditions environnementales difficiles, résister au chaud, au froid, à l'humidité, aux vibrations et à d'autres conditions extrêmes, et fournir des fonctions de contrôle précises, déterministes et en temps réel pour d'autres parties du système d'automatisation industrielle via des liaisons de communication fiables.
HMI est une interface utilisateur graphique pour le contrôle industriel. Il peut fournir une interface d'entrée de commande et de sortie de retour pour contrôler les machines industrielles. L'IHM est connectée à d'autres parties du système industriel via une liaison de communication commune.
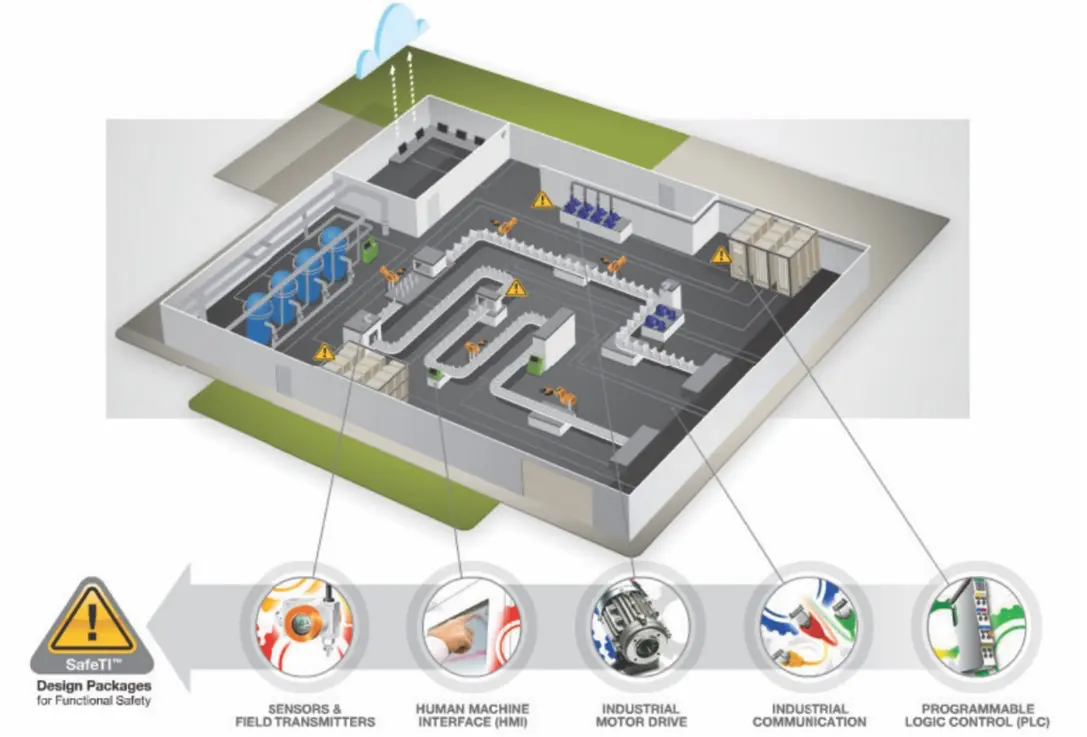
Figure 1. Éléments d'automatisation industrielle et liens de communication.
Les variateurs industriels sont des contrôleurs de moteur permettant un fonctionnement idéal du moteur. Ils sont largement utilisés dans diverses applications industrielles et peuvent prendre en charge divers niveaux de tension et de consommation électrique. Les variateurs industriels comprennent, sans s'y limiter, les variateurs CA et CC et les servomoteurs qui utilisent des systèmes de retour de moteur pour contrôler et ajuster le comportement et les performances des servomécanismes.
Les capteurs sont les mains et les pieds des systèmes d’automatisation industrielle, qui peuvent surveiller l’état des opérations industrielles, les inspections et les mesures en temps réel. Ils constituent un élément indispensable des systèmes d'automatisation industrielle et peuvent fournir des points de déclenchement et des retours pour le contrôle du système. Pour construire un système de production automatique efficace grâce à des composants industriels, une communication efficace est indispensable. L'exemple de la figure 1 illustre le principe selon lequel tous les éléments fonctionnent ensemble via un lien de communication.
Protocole de communication industriel traditionnel
Dans le passé, les gens effectuaient des communications industrielles sur des interfaces série, initialement créées par différentes entreprises et devenues plus tard des normes, de sorte que de nombreuses normes différentes sont apparues sur le marché. Étant donné que ces normes sont prises en charge par les grandes entreprises, les sociétés d'équipements d'automatisation industrielle doivent mettre en œuvre plusieurs protocoles dans un système industriel. En raison du long cycle de vie des systèmes industriels, notamment PROFIBUS ®、 Bus CAN, Modbus ® Et CC Link ® De nombreux protocoles série, y compris la configuration maître-esclave, sont toujours très populaires.
PROFIBUS est une technologie de bus de terrain la plus performante au monde, largement déployée dans les systèmes d'automatisation industrielle, notamment l'automatisation des usines et des processus. PROFIBUS fournit une communication numérique pour les données de processus et auxiliaires à des vitesses allant jusqu'à 12 Mbps et prend en charge jusqu'à 126 adresses.
Le bus CAN (Control Area Network) est un système de bus série hautement intégré. Il a été initialement créé comme bus de véhicule automatique, puis est devenu un bus de terrain pour l'automatisation industrielle. Il peut fournir une couche physique et une couche de liaison de données pour la communication série, avec une vitesse allant jusqu'à 1 Mbps. CANopen ® et DeviceNet sont des protocoles standardisés de niveau supérieur au-dessus du bus CAN, qui PEUVENT réaliser l'interopérabilité avec les appareils du même réseau industriel. CANopen prend en charge 127 nœuds dans le réseau, tandis que DeviceNet prend en charge 64 nœuds dans le même réseau.
Modbus est un bus série simple et puissant. Il est rendu public sans frais de brevet. Jusqu'à 247 nœuds peuvent être connectés dans le lien. Modbus est facile à mettre en œuvre et fonctionne sur des liaisons physiques RS-232 ou RS-485 à des vitesses allant jusqu'à 115 000 bauds. Développé à l'origine par Mitsubishi, CC Link est un protocole de réseau industriel à architecture ouverte populaire au Japon et en Asie. CC Link est basé sur RS-485 et peut connecter jusqu'à 64 nœuds dans le même réseau à une vitesse allant jusqu'à 10 Mbps.
Protocole de communication Ethernet industriel
Ethernet est omniprésent et rentable, avec des liaisons physiques communes et des vitesses plus rapides. Pour cette raison, divers protocoles de communication industriels sont transférés vers des solutions basées sur Ethernet. La communication Ethernet prenant en charge TCP/IP est généralement incertaine et le temps de réponse est généralement d'environ 100 ms. Les protocoles Ethernet industriel utilisent une couche MAC (Medium Access Control) modifiée pour obtenir une latence très faible et une réponse déterministe. Ethernet permet également au système d'avoir une topologie de réseau flexible et un nombre flexible de nœuds. Apprenons-en davantage sur certains protocoles de communication Ethernet industriels populaires.
EtherCAT a été initialement développé par Beckhoff pour prendre en charge le traitement des paquets à haut débit et fournir Ethernet en temps réel pour les applications d'automatisation. Il fournit également des connexions évolutives pour l'ensemble du système d'automatisation, depuis les grands API jusqu'aux niveaux d'E/S et de capteurs. EtherCAT est un protocole optimisé pour les données de processus, utilisant les trames Ethernet standard IEEE 802.3. Chaque nœud esclave traitera le télégramme de données et insérera de nouvelles données dans la trame au fur et à mesure du passage de chaque trame. Ce processus est traité dans le matériel, de sorte que chaque nœud nécessite un délai de traitement minimal, ce qui permet d'obtenir un temps de réponse extrêmement court. EtherCAT est un protocole de couche MAC, transparent pour tout protocole Ethernet de niveau supérieur tel que TCP/IP, UDP, serveur Web, etc. EtherCAT peut connecter jusqu'à 65 535 nœuds dans le système, tandis que le maître EtherCAT peut être un contrôleur Ethernet standard. , simplifiant la configuration du réseau. Chaque nœud esclave a une faible latence, ce qui permet à EtherCAT de fournir une solution Ethernet industrielle flexible, peu coûteuse et compatible avec le réseau.
EtherNet/IP est un protocole Ethernet industriel initialement développé par Rockwell. Contrairement à EtherCAT, qui est un protocole de couche MAC, EtherNet/IP est un protocole de couche application sur TCP/IP. EtherNet/IP utilise la couche physique Ethernet standard, la couche liaison de données, la couche réseau et la couche transport, ainsi que le protocole industriel commun (CIP) sur TCP/IP. CIP fournit un ensemble de messages et de services généraux pour les systèmes de contrôle d'automatisation industrielle, qui peuvent être utilisés pour une variété de supports physiques. Par exemple, le CIP sur le bus CAN s'appelle DeviceNet, le CIP sur le réseau privé s'appelle ControlNet et le CIP sur Ethernet s'appelle EtherNet/IP.
EtherNet/IP établit la communication d'un nœud d'application à un autre via une connexion TCP et plusieurs connexions CIP. Plusieurs connexions CIP peuvent être établies via une seule connexion TCP. EtherNet/IP utilise EtherNet et des commutateurs standard, ce qui lui confère un nombre illimité de nœuds dans le système. De cette manière, un réseau peut être déployé sur plusieurs points finaux différents de l’usine. EtherNet/IP fournit des services complets aux producteurs et aux consommateurs et peut réaliser une communication peer to peer très efficace entre les stations esclaves. EtherNet/IP est compatible avec de nombreux protocoles Internet et Ethernet standards, mais ses fonctions temps réel et déterministes sont limitées.
PROFINET est un Ethernet industriel largement utilisé par les principaux fabricants d'équipements industriels tels que Siemens et GE. Il comporte trois catégories différentes. La classe PROFINETA peut accéder au réseau PROFIBUS via un proxy et relier Ethernet et PROFIBUS avec un appel de procédure à distance via TCP/IP. Son temps de cycle est d'environ 100 ms, principalement utilisé pour les données de paramètres et les E/S cycliques. Les applications typiques incluent l’automatisation des infrastructures et des bâtiments. PROFINET classe B, également connu sous le nom de PROFINET temps réel (PROFINET RT), introduit une méthode temps réel basée sur un logiciel et réduit le temps de cycle à environ 10 ms. La classe B est généralement utilisée pour l’automatisation des usines et des processus. PROFINET Classe C (PROFINET IRT) est une transmission isochrone en temps réel, qui nécessite un matériel spécial pour réduire le temps de cycle à moins de 1 ms, afin de fournir les performances requises pour le fonctionnement de contrôle de mouvement dans Ethernet industriel en temps réel.
PROFINET RT peut être utilisé pour des applications de type automate, tandis que PROFINET IRT est très adapté aux applications sportives. Les branches et les étoiles sont des topologies courantes de PROFINET. Si vous souhaitez que le réseau PROFINET atteigne les performances système requises, vous devez planifier soigneusement la topologie.
POWERLINK a été initialement développé par B&R. Ethernet POWERLINK est adopté sur IEEE 802.3, de sorte que la topologie du réseau, la connexion croisée et la connexion à chaud peuvent être librement sélectionnées. Il utilise des mécanismes d'interrogation et de découpage temporel pour réaliser un échange de données en temps réel. La station maître POWERLINK ou « nœud géré » contrôle la synchronisation temporelle en quelques dizaines de nanosecondes grâce à la gigue des paquets. Ce type de système s'applique à divers systèmes d'automatisation allant de la communication et de la visualisation PLC à PLC au contrôle de mouvement et d'E/S. Un logiciel de pile open source est disponible, il y a donc peu d'obstacles à la mise en œuvre de POWERLINK. De plus, CANopen est un composant standard, ce qui facilite la mise à niveau du système à partir du protocole de bus de terrain précédent. Sercos III est le système de communication série en temps réel (Sercos) de troisième génération. Il combine des capacités de traitement de paquets à haut débit pour fournir des communications Ethernet en temps réel et TCP/IP standard afin de créer un Ethernet industriel à faible latence.
Tout comme EtherCAT, les paquets de données sont traités depuis Sercos III en extrayant rapidement les données et en les insérant dans des trames Ethernet pour obtenir une faible latence. Sercos III divise les données d'entrée et les données de sortie en deux trames. Le temps de cycle commence à 31,25 microsecondes, ce qui est aussi rapide qu'EtherCAT et PROFINET IRT. Sercos III prend en charge la topologie en anneau ou en ligne. L’un des principaux avantages de l’utilisation d’une topologie en anneau est la redondance des communications. Même si l'anneau est rompu en raison d'une défaillance d'un nœud esclave, tous les autres nœuds esclaves peuvent toujours obtenir des trames Sercos III contenant des données d'entrée/sortie. Sercos III peut avoir 511 nœuds esclaves dans un réseau, principalement utilisés pour le contrôle des servomoteurs.
Time Sensitive Network (TSN) est une extension d'Ethernet définie par l'Institute of Electrical and Electronics Engineers (IEEE), visant à rendre le réseau Ethernet plus déterministe. TSN est une solution de niveau réseau local (LAN) qui peut fonctionner avec Ethernet non TSN, mais la rapidité ne peut être garantie qu'au sein du LAN TSN. Vous pouvez regrouper les standards TSN selon les cas d'usage résolus par TSN : vue temporelle générale, grand délai garanti, ou coexistence avec du trafic de fond ou autre. Comme toute norme populaire, la boîte à outils standard de TSN évolue également.
Mécanisme de communication industrielle de Texas Instruments (TI)
Afin de permettre aux fabricants d'équipements industriels de mettre en œuvre divers protocoles de communication industrielle de manière économique et flexible, Texas Instruments (TI) a intégré un sous-système de communication industrielle unitaire en temps réel programmable à faible latence (PRU-ICSS) sur une variété de puces. systèmes. Comparé aux FPGA, ASIC et autres solutions de sauvegarde, PRU-ICSS peut fournir des solutions flexibles plus rentables et orientées vers l'avenir pour les communications industrielles. En intégrant PRU-ICSS dans une seule puce, la plate-forme matérielle flexible de TI aide les fabricants à créer des systèmes d'automatisation industrielle programmables par logiciel plus rentables, déterministes et efficaces.
Tendances futures
Nous sommes au début de la quatrième révolution industrielle et l’automatisation industrielle redeviendra un facteur moteur du développement économique. Le succès de l’automatisation industrielle dépend de réseaux de communication fiables et efficaces qui relient toutes les parties de l’usine pour un fonctionnement efficace. La popularité et l'applicabilité d'Ethernet continueront à inciter les usines traditionnelles à passer à l'Ethernet industriel.
De nombreux protocoles Ethernet industriels différents ont été mis en œuvre sur site, et chaque protocole présente ses propres avantages et inconvénients. À l'avenir, les protocoles Ethernet industriels continueront à se développer et à s'intégrer pour créer un lien de communication en temps réel, déterministe et stable avec une fiabilité plus élevée et une sécurité intégrée. Ethernet nécessite également une plate-forme matérielle programmable générale, telle que Sitara avec processeur PRU-ICSS intégré introduit par le processeur Texas Instruments (TI) ™ pour construire des systèmes flexibles à faible coût. Le système prend en charge la mise en œuvre prospective de plusieurs protocoles et de nouveaux protocoles, et peut fournir un moteur de communication industrielle pour l'automatisation industrielle.